
Four-Bar Linkage Mechanism
Course: ME 350
Team Size: 4 people
Goals
- "To design, build, and test a powered mechanism that will automatically pick up and sort disks based on their color."
- Maximize points scored due to disk dropping location, sorting accuracy, and time to deposit all 18 disks.
Design Process
1. Design Goals & Requirements
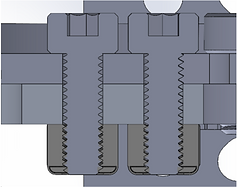
Hard Requirements Soft Requirements
• Deviation of transmission angle: 0 to 60°
• Sorting accuracy: 100%
• Total points: 420
• Repeatability: <40 point deviation between trials
• Time for Assembly: 40 to 90 minutes
• Durable
• Easy to assemble
• Safe to operate

2. Design Selection
Linkage synthesis (SOLIDWORKS): All team members developed a unique path over the different color zones.
Analysis (ADAMS): The four designs were tested for metrics such as power, velocity, and torque generation.
Pugh chart: All designs were compared based on our requirements and the team decided to create a new design using the best features of each.
3. Prototype Development
CAD model (SOLIDWORKS): Every component was assembled and mated for a movable model. A new iteration fixed interfering components and optimized joint design.
Transmission design: The optimal value of transmission ratio was selected based on the electromagnetic resolution.
Physical model: A four-bar linkage was assembled individually by each team member including a color sensor, Arduino board, motor with digital encoder, and an electromagnet. The design was adapted based on the experienced design for assembly issues.
Full automation: The mechanism was fully automated by programming the Arduino and calibrating the color sensor, encoder positions, and electromagnet levels.

4. Testing
Trials: Multiple trials were conducted and the results were observed. The mechanism was improved to better meet the goals with changes such as altering angle and height of the mechanism, re-calibrating the color sensor, and re-programming the Arduino.
Challenges
- Due to COVID-19: constrained to the materials in the provided project kit and no opportunity to machine parts.
- Iterative process limited by the course end date.
Results
- Deviation of transmission angle: 27.35°
- Sorting accuracy: 100%
- Total points (average between team members): 550
- Repeatability: 60 point deviation between trials
- Time for assembly: 120 minutes
- Durable, easy to assemble, and safe to operate
Conclusion
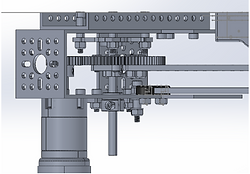

Overall, the team performed very well and all goals were met. All of the soft design requirements and most of the hard design requirements were met. The repeatability and time for assembly results were below expected, however further iterations and experience with assembling could have resolved these issues.
This project was my first experience with mechatronics and I both enjoyed and learned so much from it. I experienced first-hand the balance between precision and accuracy when engineering to deposit the disks. Due to the remote learning format preventing most teamwork, I was required to participate in all parts of the design cycle and gained empirical knowledge of designing a powered mechanism.